British luxury motor manufacturer selects KIT for efficient calibration management
A British luxury motor manufacturer, renowned for its commitment to precision and quality, needed to ensure that their tool and equipment calibration processes were as robust as possible, whilst also enhancing how they managed and maintained their extensive array of calibrated tools and equipment.
A decision was made to partner with Coplan to implement KIT, a comprehensive calibration management solution designed to streamline the processes around prompting the collection and return of tooling and equipment amongst users whilst also offering a dynamic test and validation solution for internal validation of items.
KIT is a web-based and mobile application designed to streamline the calibration process, enhance accuracy, and provide a centralised system for tracking tools and equipment.
"KIT has empowered this motor manufacturer to elevate its calibration management processes, providing a scalable and customised solution that meets their very specific and unique needs.
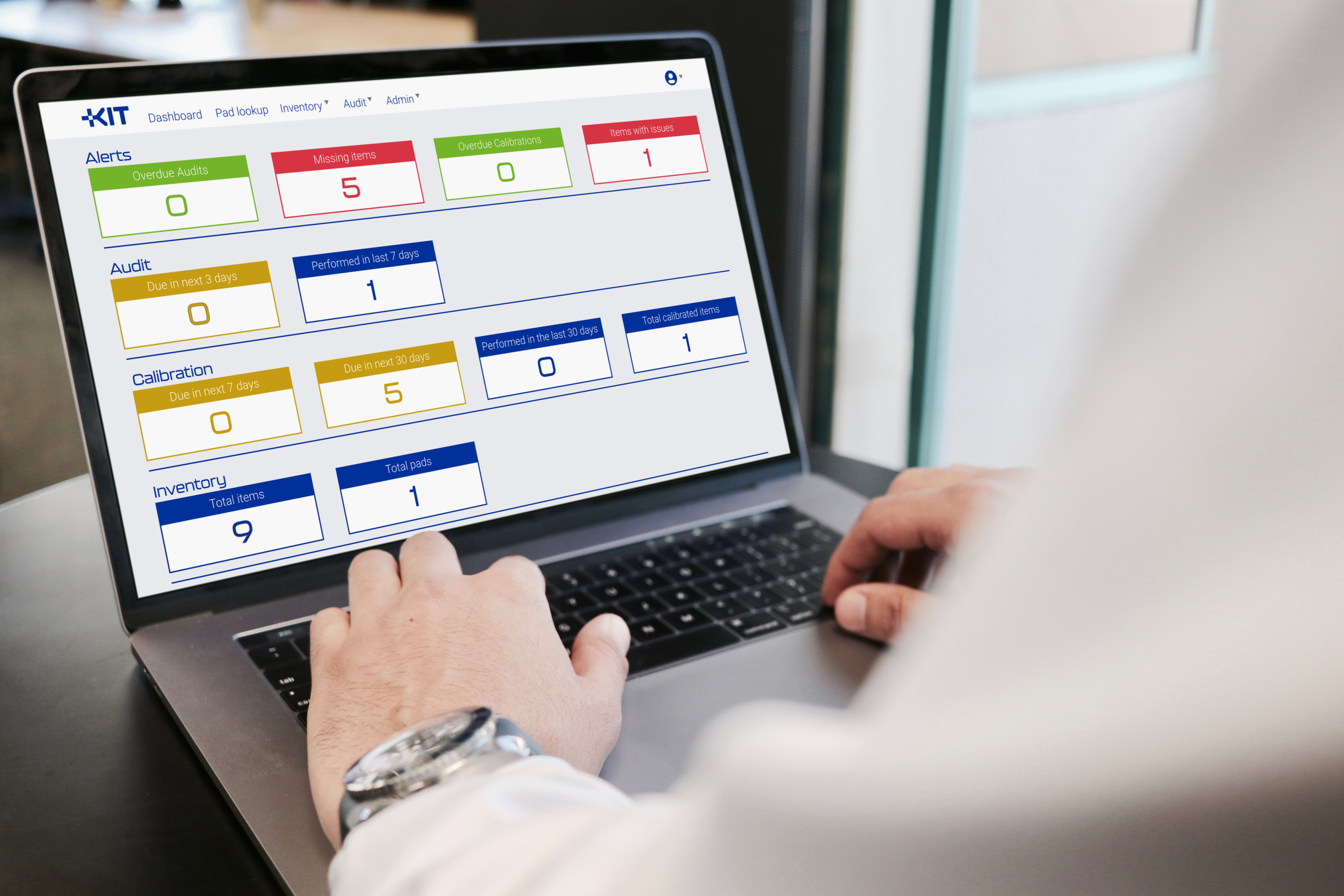
What are the key features and benefits of the system?
Instant tool identification
Any tool or piece of equipment can be swiftly identified by scanning the attached barcode within the KIT application.This grants instant access to the calibration status, home location, owner(s) and other pertinent information. This streamlined process enhances efficiency and reduces downtime particularly when searching for and identifying tools ‘on the line’.
Calibration tests and validation
KIT enables users to create and publish the testing parameters for their calibrated tooling and equipment. The team are then able to perform validation checks on tooling and input the results. KIT cross-references the results against the parameters and then provides a detailed report for each and every test performed. The system offers a complete calibration history for every tool.
Reporting and reminders
KIT provides prompts and reminders via the system dashboard and notification emails, to ensure all appropriate parties are aware of equipment requiring calibration and the actions required to be taken. The system automates the traditional administrative task of notifying tooling and equipment owners to either arrange for their equipment to be ‘dropped off’ or collected as necessary, enabling teams to focus on the more proactive and appropriate tasks
KPI reports are also generated to provide the senior teams with an overview of performance, achievements and areas for improvement.
Return on Investment
Implementing KIT has resulted in a significant time saving for this manufacturer, through the reduction of manual administrative tasks typically associated with ensuring performance and compliance. Manual prompts and reminders have been replaced by automation whilst the ease of data access through in-app scanning reduces the time spent identifying tooling and equipment.
The company already maintained the highest standards for these critical processes and have looked to improve these further by utilising the efficiency, reliability and scalability of KIT.
Centralised data
The system infrastructure is built on the latest technology with system speed and ease-of-use of paramount importance. This approach facilitates easy access to and retreival of crucial information for the calibration process and operations.
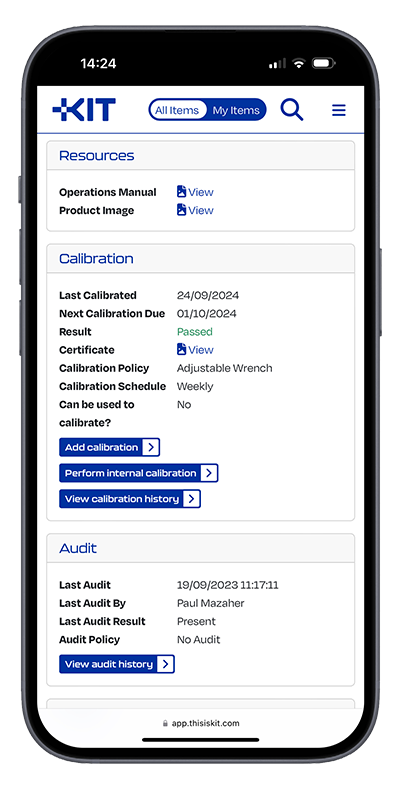
KIT has empowered this British luxury motor manufacturer to elevate its calibration management processes, providing a scalable and customised solution that meets their very specific and unique needs. The implementation of KIT has not only improved efficiency but has also established a new standard for precision and accountability within the company’s tool calibration practices.
Want to know more?
For more information on how KIT and Coplan can help you standardise items in your organisation.
Call us today on +44 (0)1234 943700 or email us on sales@thisiskit.com