When 5S isn’t 5S, it’s only 3S
How KIT helps organisations achieve full 5S
The 5S methodology is a cornerstone of workplace organisation, focusing on Sort, Set in Order, Shine, Standardise, and Sustain. While many organisations excel at the first three steps, they often fall short on the final two. Without proper standardisation and sustainability, the benefits of 5S are fleeting.

Enter KIT, a transformative system that leverages QR codes and a centralised database to ensure organisations don’t just reach 5S, but maintain it for the long term. KIT bridges the gap between 3S and 5S, making true workplace efficiency and consistency achievable.
Why do organisations get stuck at 3S?
It’s common for organisations to start strong with 5S, achieving tidy and organised workspaces. However, many struggle to move beyond the first three steps. Let’s explore why:
1. Missing tools lead to delays
Tools often go missing due to lack of tracking, creating inefficiencies. Employees spend valuable time searching for items, disrupting workflows.
2. Inconsistent tool replacements cause disorder
When tools are damaged or lost, replacements are frequently purchased without adherence to standards. This results in mismatched tools that disrupt the system.
3. No documented processes to maintain standards
Without clear procedures for tool management, teams often revert to old habits. This lack of standardisation means the workspace becomes disorganised again over time.
These common issues illustrate why Sort, Set in Order, and Shine are not enough to achieve lasting results.
How KIT bridges the gap between 3S and 5S
KIT transforms how organisations manage their tools and workspaces, addressing the critical gaps in Standardise and Sustain. Here’s how it works:
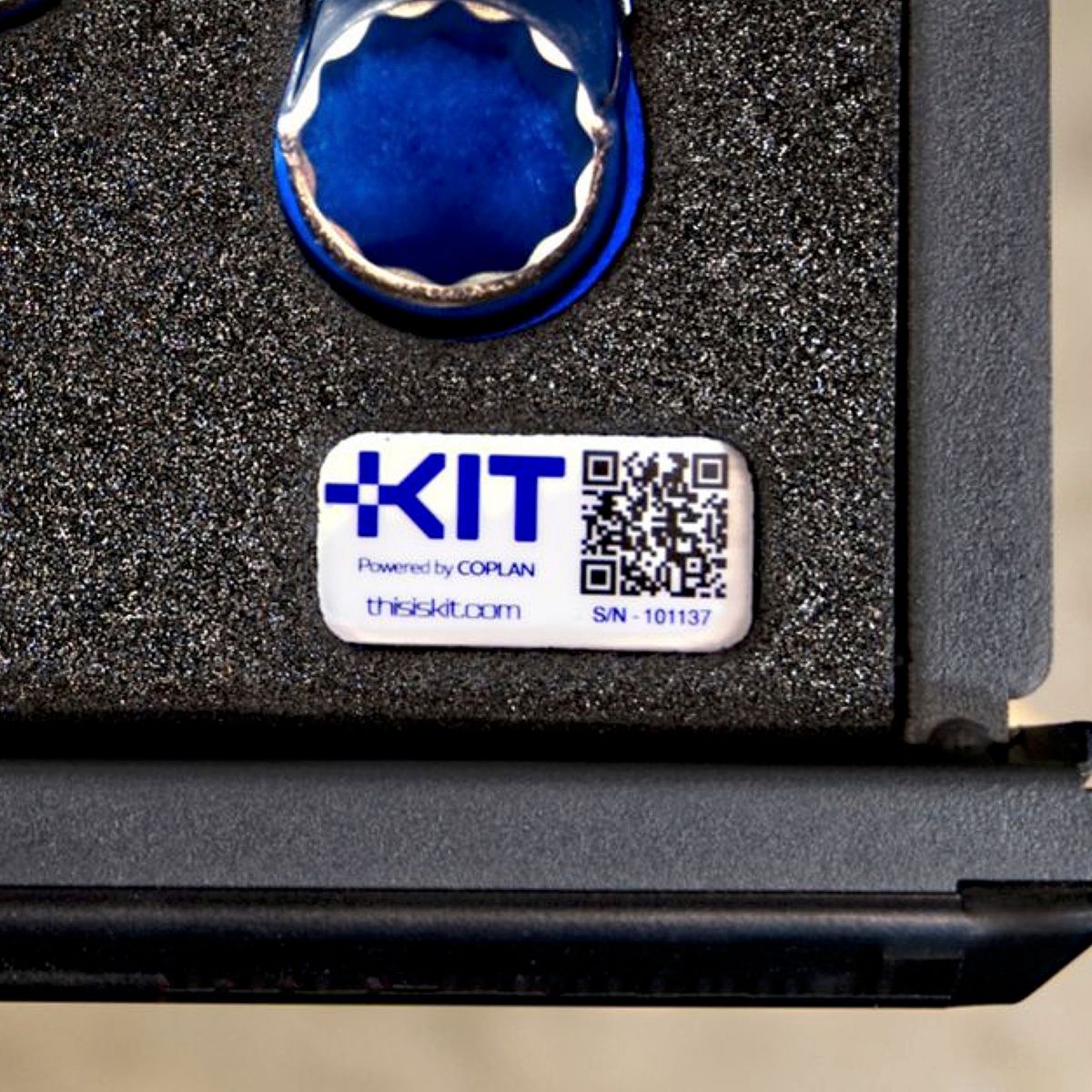
1. QR codes for efficient tool tracking
Every tool in your workspace is assigned a unique QR code linked to KIT’s centralised database. This system provides:
- Instant Location Tracking: Employees can scan QR codes to locate tools or report missing items.
- Accountability Across Teams: Usage can be monitored to ensure tools are returned to their proper place.
- Streamlined Audits: Routine checks become faster and more accurate with a simple scan.
2. A centralised database for standardisation
KIT’s database acts as the foundation for consistent tool management. It includes:
- A full inventory of all tools, their specifications, and maintenance requirements.
- Clear guidelines for ordering replacements, ensuring that new tools match the originals.
- Documentation of standard operating procedures, accessible to all employees.
3. Automated processes for sustainability
Sustainability requires ongoing effort, and KIT makes it easy to maintain high standards. Key features include:
- Automatic Alerts: Notifications remind teams to reorder tools or perform maintenance.
- Regular Reports: Data insights highlight trends, such as frequently misplaced tools, enabling proactive solutions.
- Customisable Checklists: Ensure teams follow 5S principles consistently.
"It’s common for organisations to start strong with 5S, achieving tidy and organised workspaces. However, many struggle to move beyond the first three steps.
From 3S to 5S: why KIT is the missing piece
For organisations relying on foam shadow boards or manual tracking systems, KIT provides the tools needed to reach and maintain full 5S. Here’s what sets KIT apart:
1. Solves the problem of missing tools
With QR code tracking, every tool is accounted for. Teams can quickly identify and address missing or misplaced items, reducing downtime.
2. Ensures consistency across the workspace
KIT’s centralised database eliminates inconsistencies caused by ad-hoc replacements. Every tool is standardised to fit the system, ensuring a logical and efficient setup.
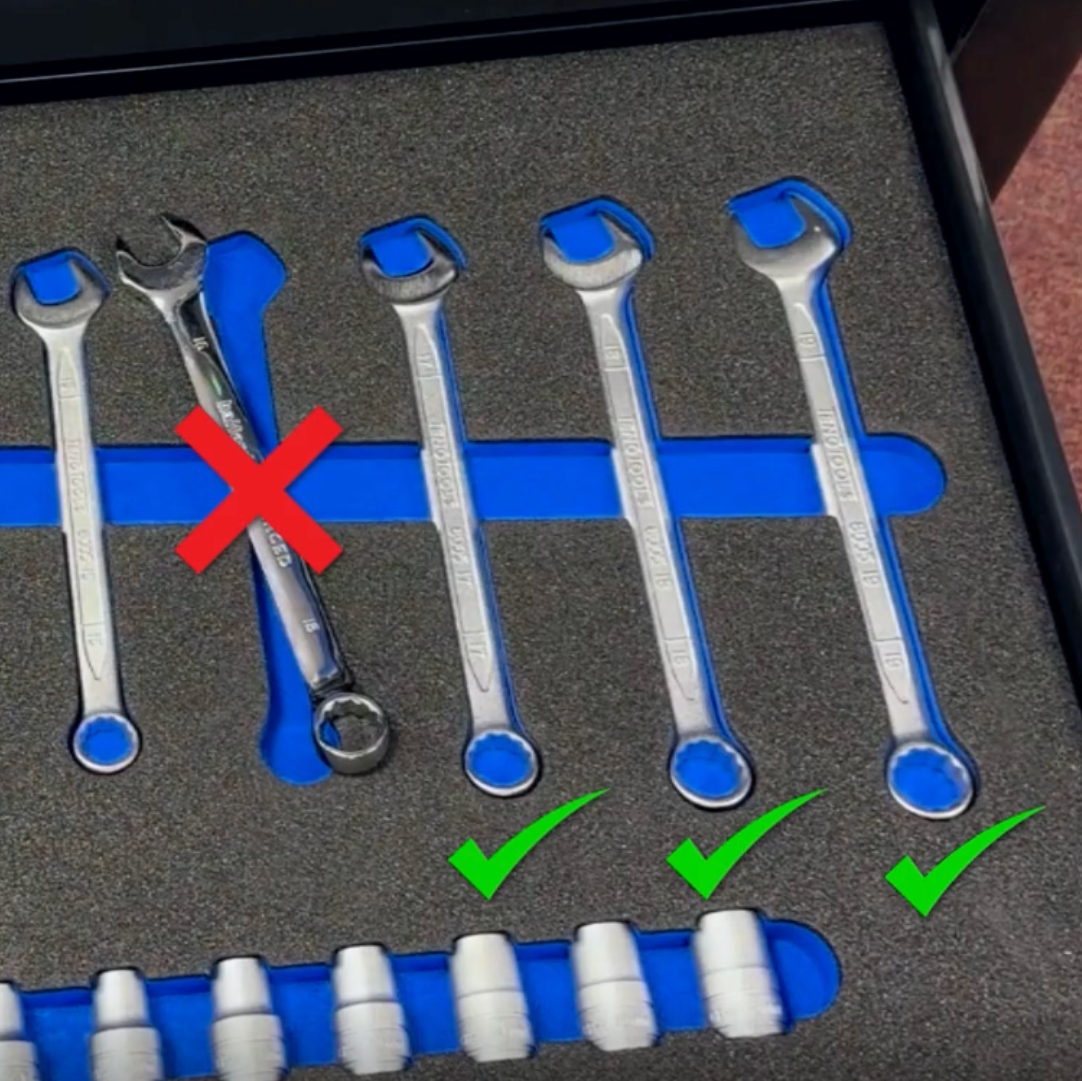
3. Embeds sustainability into daily operations
KIT empowers teams to sustain 5S practices with automated reminders, reports, and an intuitive interface. This ensures 5S becomes a long-term habit, not just a temporary improvement.
KIT in action: realising the full potential of 5S
Imagine a workspace where tools are always accounted for, replacements are consistent, and teams are equipped with the data they need to improve. KIT makes this vision a reality by addressing the weaknesses in traditional 3S systems.
With KIT, you’ll experience:
- Faster workflows with minimal downtime caused by missing tools.
- A culture of accountability, where employees take ownership of their workspace.
- Long-term benefits of 5S, including improved safety, efficiency, and organisation.
Achieve true 5S with KIT
If your organisation has struggled to maintain 5S or has found its efforts stalling at 3S, KIT is the solution you need. With its innovative QR code technology and centralised database, KIT bridges the gap, helping organisations move from short-term fixes to long-term success.
Take the next step toward workplace excellence. Visit thisiskit.com to learn how KIT can help your organisation achieve and sustain true 5S.